Beehive Industries® CEO Mohammad Ehteshami Delivers America’s Next Defense Solution
100% American-made jet engine fires up in Denver headquarters.
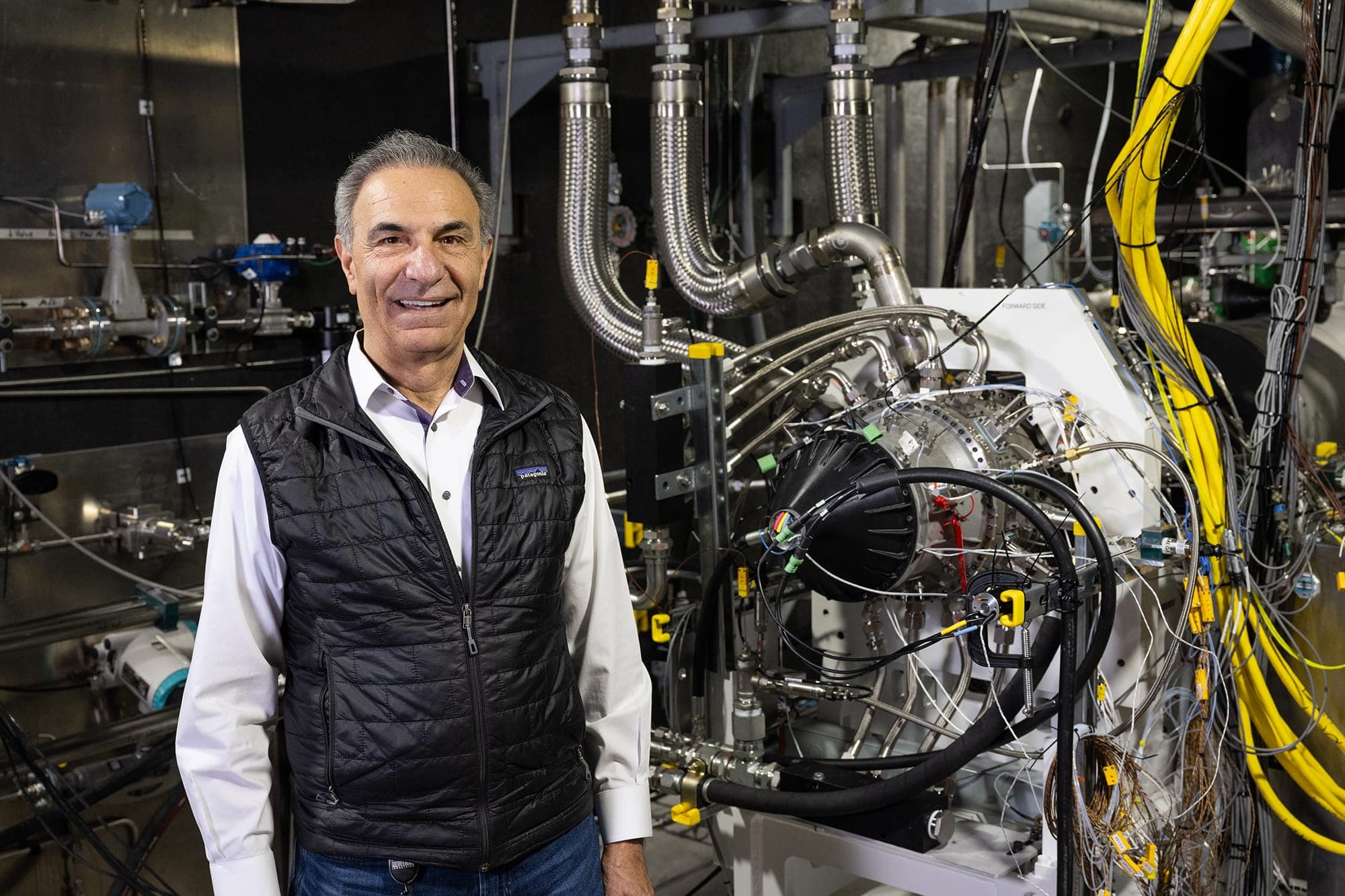
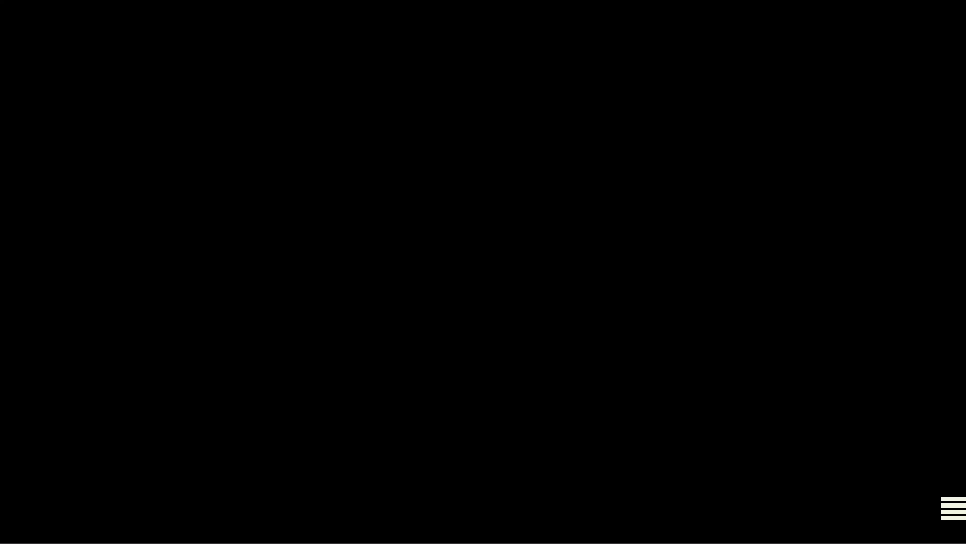
Beehive Industries® CEO Mohammad Ehteshami has worked in the aerospace industry for over 40 years, building jet engines. But his proudest achievement isn’t an engine. It’s the team he built at Beehive.
That team has designed and delivered a 500 lbf jet engine built with additive manufacturing (3D printing). This engine, specifically designed for defense applications, is a significant milestone. Designing and manufacturing with additive has allowed the Beehive team to rapidly produce an engine that offers improvements across the board.
Speaking from the manufacturing floor, Ehteshami breaks into a big smile when asked about the team.
“The best product Beehive has produced is our team, and I couldn’t be prouder,” said Ehteshami. “That’s what has made the engine possible. We brought together engineers and experts from different backgrounds, from large OEMs to startups, and asked them to work together in a new way. We don’t silo design, manufacturing, and assembly. We’re all one team. I do not doubt that many more engines and breakthroughs will come out of this team.”
The Beehive origin story
Beehive began with Ehteshami seeing a problem. That problem was the cost of producing jet engines for U.S. defense applications and the time required to deliver engines. Traditional manufacturing was, and still is, too costly and slow. He believed that additive manufacturing could change both.
“We identified a need within the defense sector to disrupt the cost and speed of jet engine manufacturing,” explains Ehteshami. “Following extensive research, we determined that we could produce an engine in a fraction of the time and at a portion of the cost with additive manufacturing. Most importantly, we knew we could do it all in the U.S.”
Using additive manufacturing to accelerate production became Beehive’s focus, but the team knew that additive could deliver more significant benefits. The result is a 500 lb thrust jet engine demonstrator, the first in a suite of propulsion systems. This engine, with its versatility and adaptability, has the potential to power a wide range of defense applications. Close to 90% of the demonstrator is manufactured with additive.
Speed, cost, quality, and consolidation
Ehteshami breaks down the benefits of additive into four categories.
Speed. Manufacturing with additive reduces the life cycle of development, production, assembly, and testing by half. By accelerating production with additive, Beehive can deliver a new engine significantly faster than traditional manufacturing.
Cost. An additively enabled engine has dramatically fewer parts. Compared to traditional jet engine manufacturing, an additively enabled engine will only have approximately 10 percent of the parts. In addition to fewer parts, designing for additive reduces the number of assemblies, significantly reducing post-production processes and touch time.
Quality. Beehive controls all aspects of the production process. Beehive designs, prints, machines, assembles, and tests engines in-house to meet the specific requirements of the applications they power.
Consolidation. Not only are parts consolidated, but so is the supply chain. Beehive controls every aspect of production, eliminating the opportunity for disruption from third-party suppliers.
This level of control and efficiency is not limited to the demonstrator engine. Beehive envisions a future where additive manufacturing benefits the entire aerospace industry, from small components to large structures, making production faster, more cost-effective, and more easily modified.
Ehteshami also stresses an advantage beyond cost savings, time to delivery, and performance. He emphasizes that Beehive engines are 100% American-made. Each engine is designed, manufactured, assembled, instrumented, tested, and inspected inside one of Beehive’s U.S. facilities.
“We want American troops to have what they need when they need it, and we know we can accelerate more and better propulsion for America’s defense,” explains Ehteshami. “Our engines will power drones, UAVs, and missiles, providing a deterrent to our enemies and an advantage to our troops on the ground, in the air, and at sea.”
Lighting the spark
The Beehive team designed and built the engine and the test cells used for First Engine to Test (FETT), an extensive testing process for new engines.
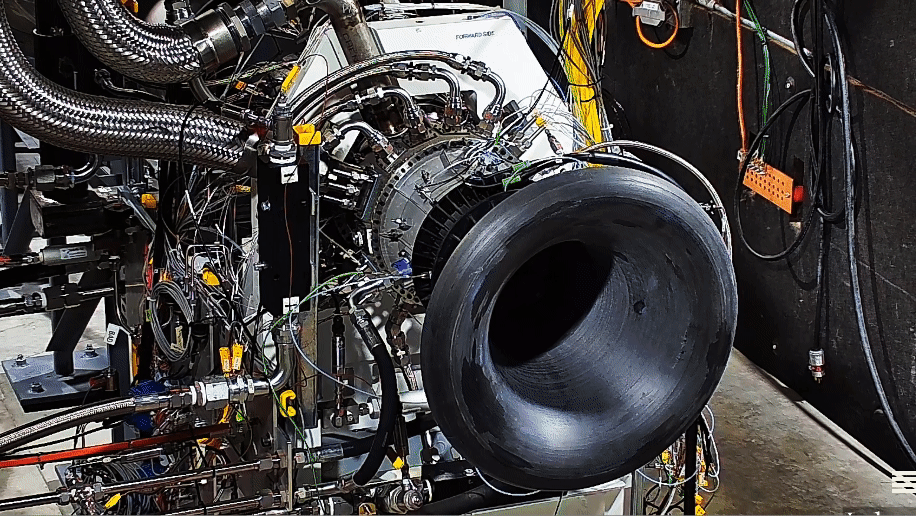
“We use First Engine to Test for data acquisition to refine the design and inform future designs,” explains Ehteshami. “Before we start the engine, we test everything in the test cell: lubrication, fuel, dry motoring, wet motoring, fluid and air delivery, and much more. Then, we spin the engine to speed, and introduce fuel and ignite it or and spark ignition or and light it up. Throughout, we’re watching hundreds of instrumentations to monitor engine behavior–vibration, stresses, temperature, speed, you name it. Then, we repeat.”
During testing, the Beehive team examines the results against their expectations. Then, they apply what they have learned to improve and enhance engine design and the manufacturing process.
“While First Engine to Test of the demonstrator has been a thrilling experience, what I value most about this journey is working with the team each day,” continues Ehteshami. “When we built the team, we weren’t sure we could get to where we are today. We adopted an approach that “impossible” is just an opinion, and we learned a new way of collaborating and working together as a combined engineering and manufacturing team.
“The Beehive team not only pushes each other in a spirit of collaboration, they also push me,” concludes Ehteshami. “They challenge me on decisions, and I love it.”