Capacity, Capability, and People: What Fuels Beehive Industries® COO Darius Ehteshami
Darius Ehteshami talks solving America’s supply chain problem to support military readiness.
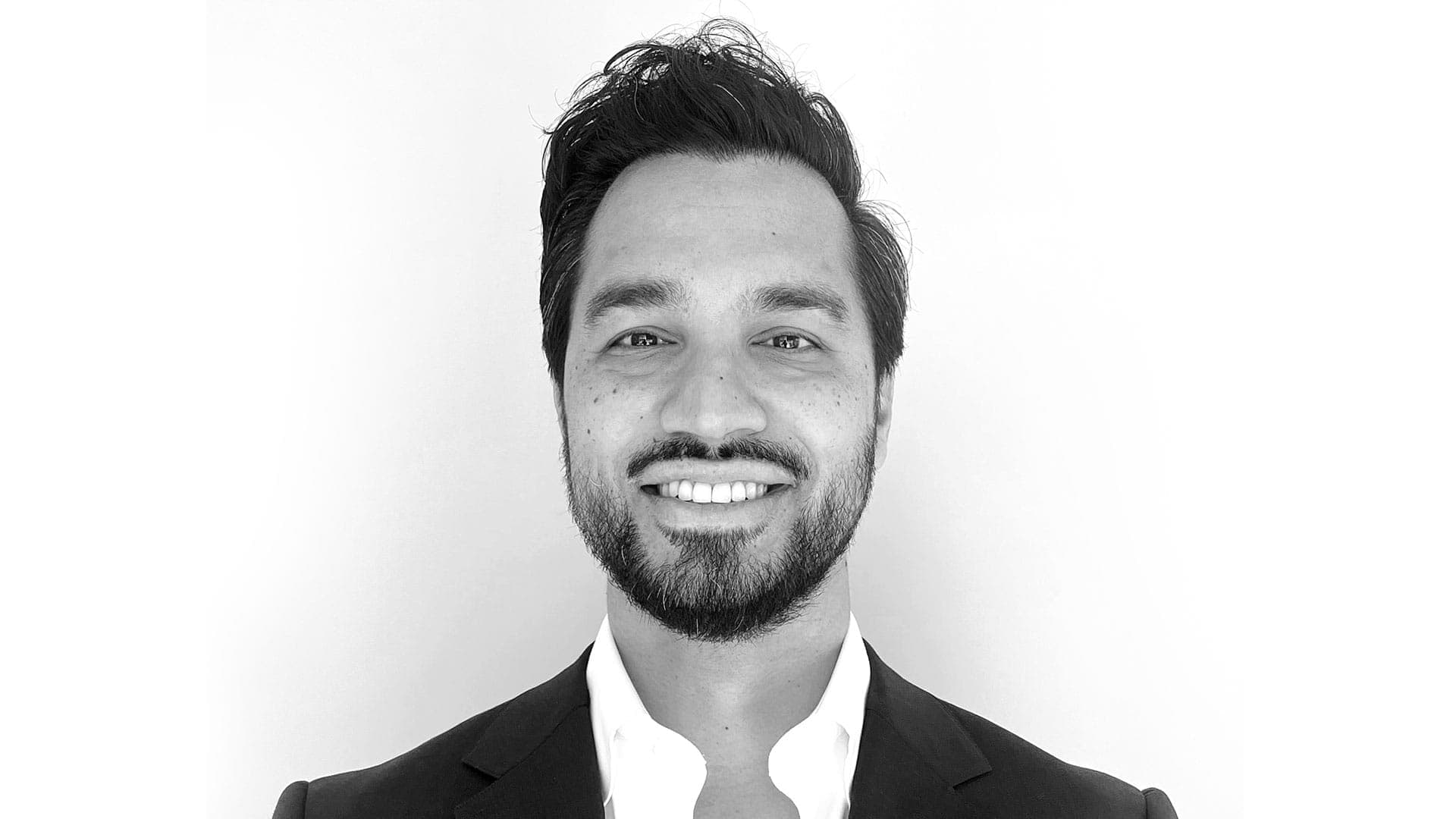
The supply chain problems impacting American defense weigh heavily on Darius Ehteshami, COO of Beehive Industries®. But, he knows the solution is in sight.
Ehteshami is laser-focused on a single goal: breaking the production barrier for military jet engines. Like the rest of his team, he believes the key is additive manufacturing (3D printing). With this technology, Beehive will eliminate the complexities of the supply chain.
Simplifying to the extreme
Traditionally, America and its allies rely on a complex, costly, and potentially vulnerable network of international suppliers and manufacturers. It can take years to design, test, and manufacture a new engine due to the players involved, which puts the U.S. at a disadvantage. Today, production can’t meet demand, and delivery dates are unreliable.
At Beehive, Ehteshami and his team are working to eliminate that global supply chain and complex manufacturing process.
“We’re simplifying to the extreme with additive manufacturing,” explains Ehteshami. “We’re simplifying design, supply chain, manufacturing, post-processing, and testing. We’re applying the benefits of additive throughout. At the same time, we’re doing it leaner. We have the capacity and capability to deliver jet engines faster, cheaper, and in greater quantities to meet the immediate needs of the Department of Defense.”
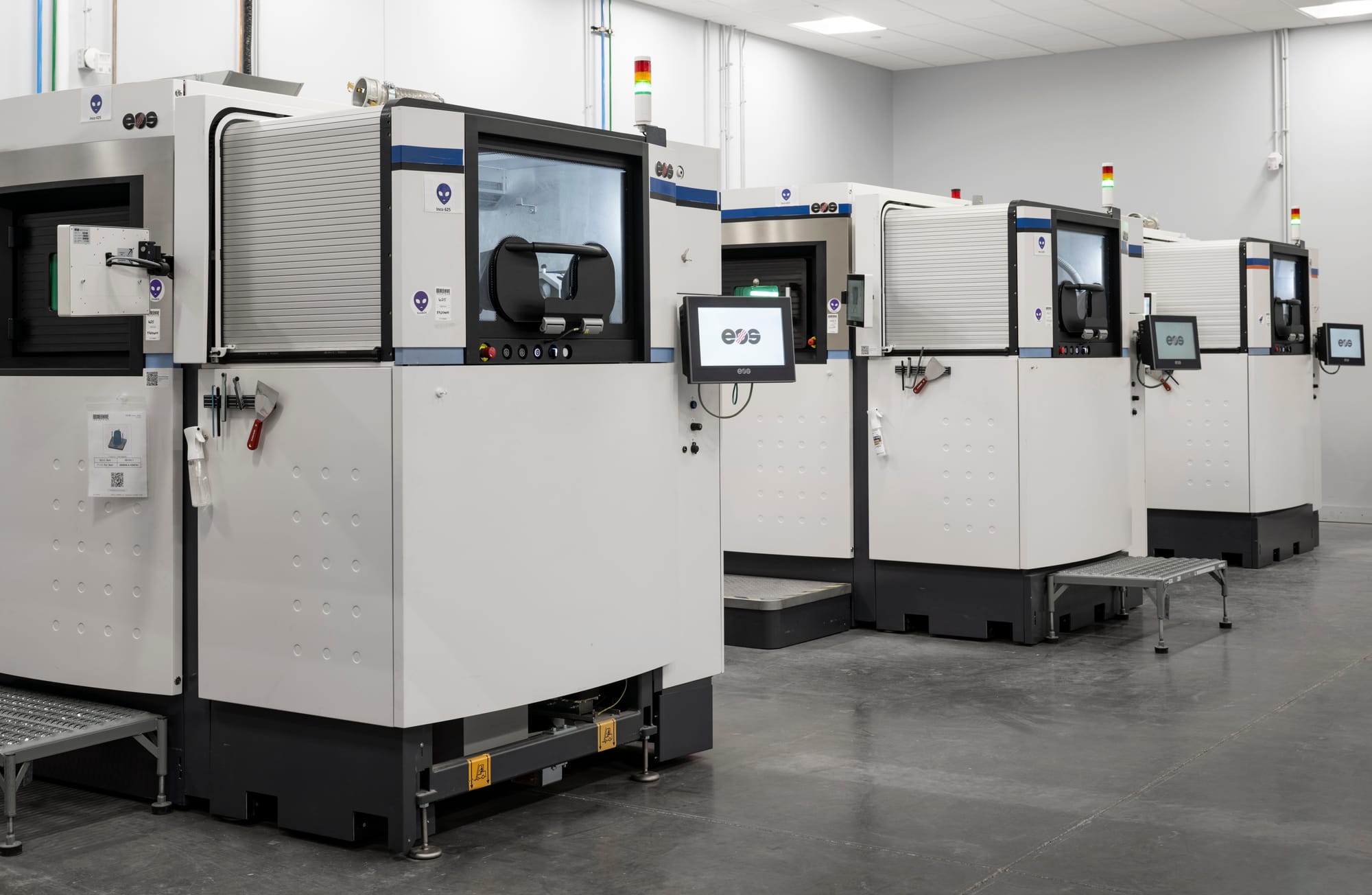
With additive, Beehive can produce thousands of engines for munitions and unmanned aerial vehicles (UAVs) annually on U.S. soil. The result will be improved military readiness, ensuring that America’s troops have the equipment to respond to threats and emergencies without delay.
According to Ehteshami, Beehive’s approach to simplifying the supply chain is a radical change in mindset.
The affordable mass problem
Taking a step back, Ehteshami shared why Beehive’s solutions are a sea change.
“Historically, American defense relied on a variable network of organizations that spanned multiple countries and continents for the design, testing, and production of its jet engines, which had hundreds of parts,” explains Ehteshami. “Even the smallest issue disrupts that supply chain. At the same time, the complex nature of older engine designs adds layers of unknowns. With hundreds of components, many requiring castings and forgings, testing and production were burdensome and expensive.”
What results from a traditional manufacturing approach? Delays, cost overruns, compromises, and an affordable mass problem. Traditional manufacturing can’t produce attritable propulsion systems in the quantity needed and at the required cost.
Ehteshami has made it his personal mission to apply all the benefits of additive manufacturing to solve this problem.
Today, Beehive can design, test, and manufacture attritable jet engines on U.S. soil. They’re doing it faster and cheaper than traditional manufacturing, effectively upending how the industry has plodded along for close to 100 years.
No more trade-offs
“Traditionally, there were trade-offs in engine design,” said Ehteshami. “Manufacturers compromised performance (thrust), weight (fuel consumption), and cost. There was an ‘old world’ approach based on producing engines that would be in operation for years to carry people. They are still applying the same approach to drone engines as engines for commercial jets. That meant substantially higher costs that deliver no additional value or performance benefits for their intended purpose in drones and munitions. It’s needless waste.”“Unlike traditional manufacturing, Beehive isn’t constrained by the same conventional design and manufacturing methods,” continued Ehteshami. Beehive engines can offer better performance, lower weight, and lower cost. Thanks to additive manufacturing, we can manufacture engines at scale to rapidly meet demand.”
Ehteshami explained that Beehive can condense the manufacturing process of a traditional jet engine, which has nearly 80 parts and more than 200 steps in a multi-layer supply chain, into a single printer in one of its three U.S. facilities.
Beehive designs, prints, and tests more than 90% of its engines in the company’s Colorado, Ohio, and Tennessee facilities. The team can get an engine into a test cell within months and begin testing on-site, enabling them to determine the ideal balance between performance, weight, and cost—while not making compromises.
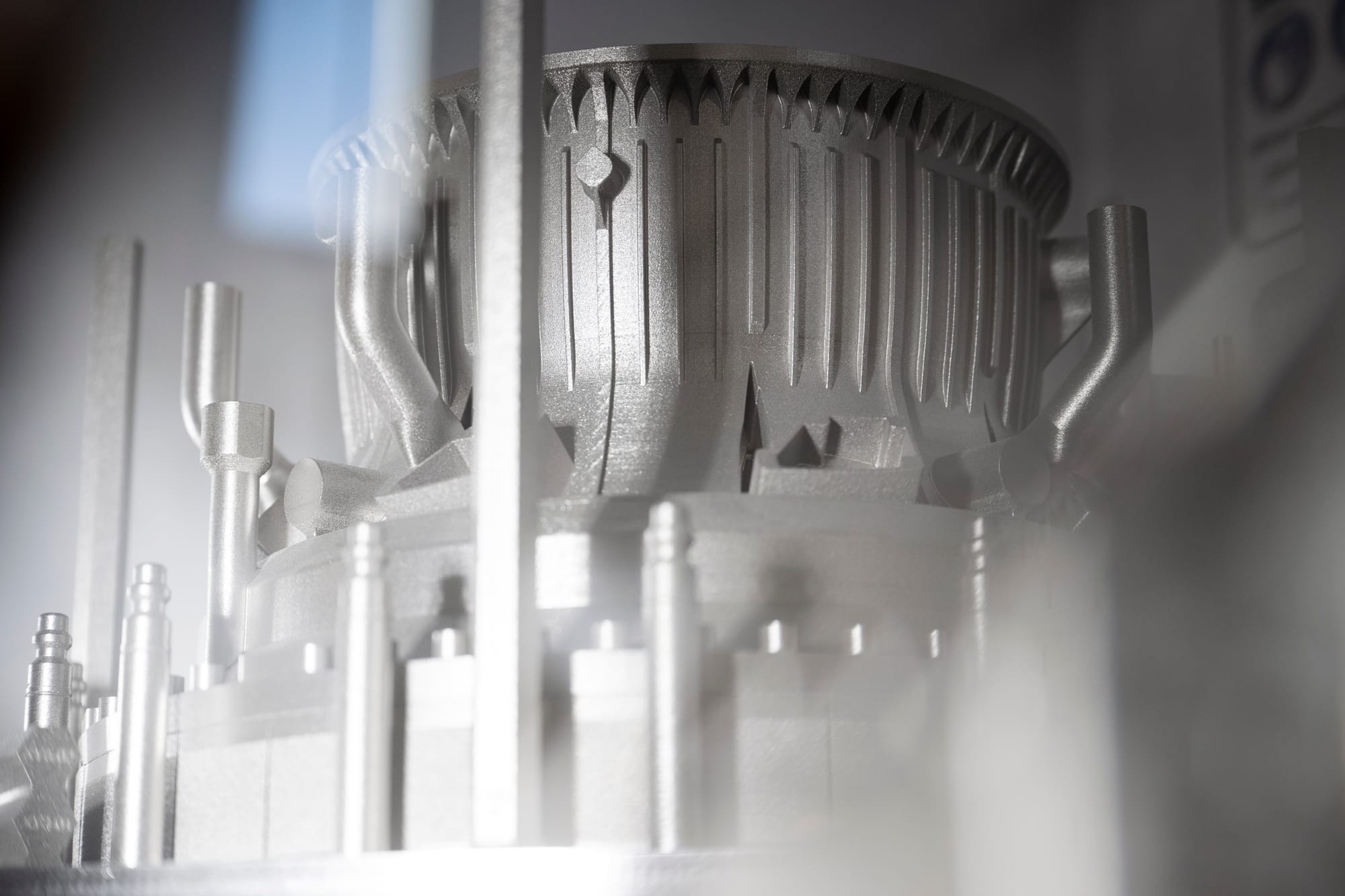
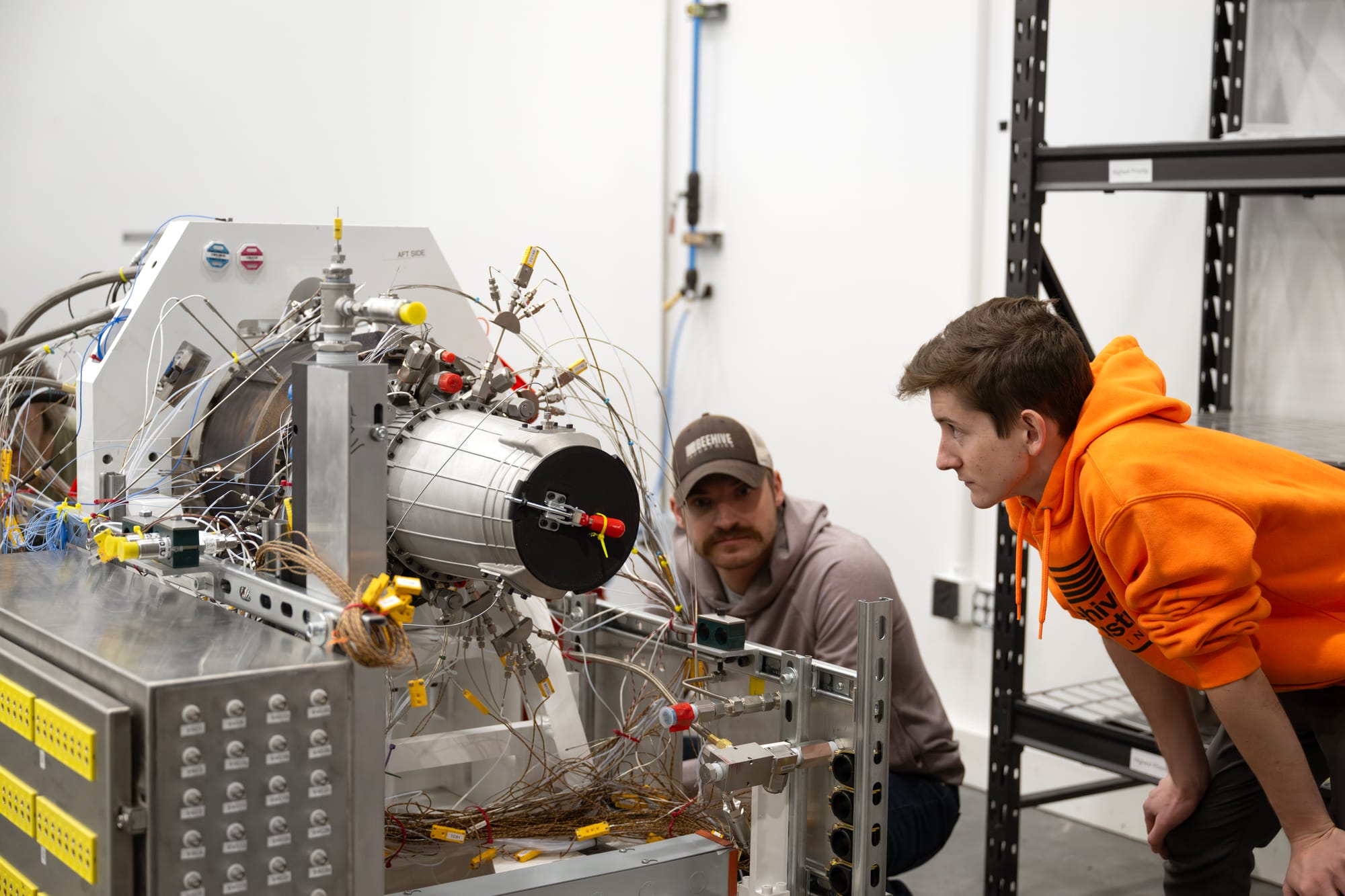
Beehive's engines can be produced at scale, potentially reaching hundreds a month, providing an affordable and reliable defense solution for U.S. troops and allies. By simplifying the supply chain to the extreme with additive, Beehive can deliver more capacity, greater security, and improved performance, on U.S. soil.