Right Place, Right Time for Eric Donovan
Advancements in additive manufacturing and computing make what was once impossible possible.
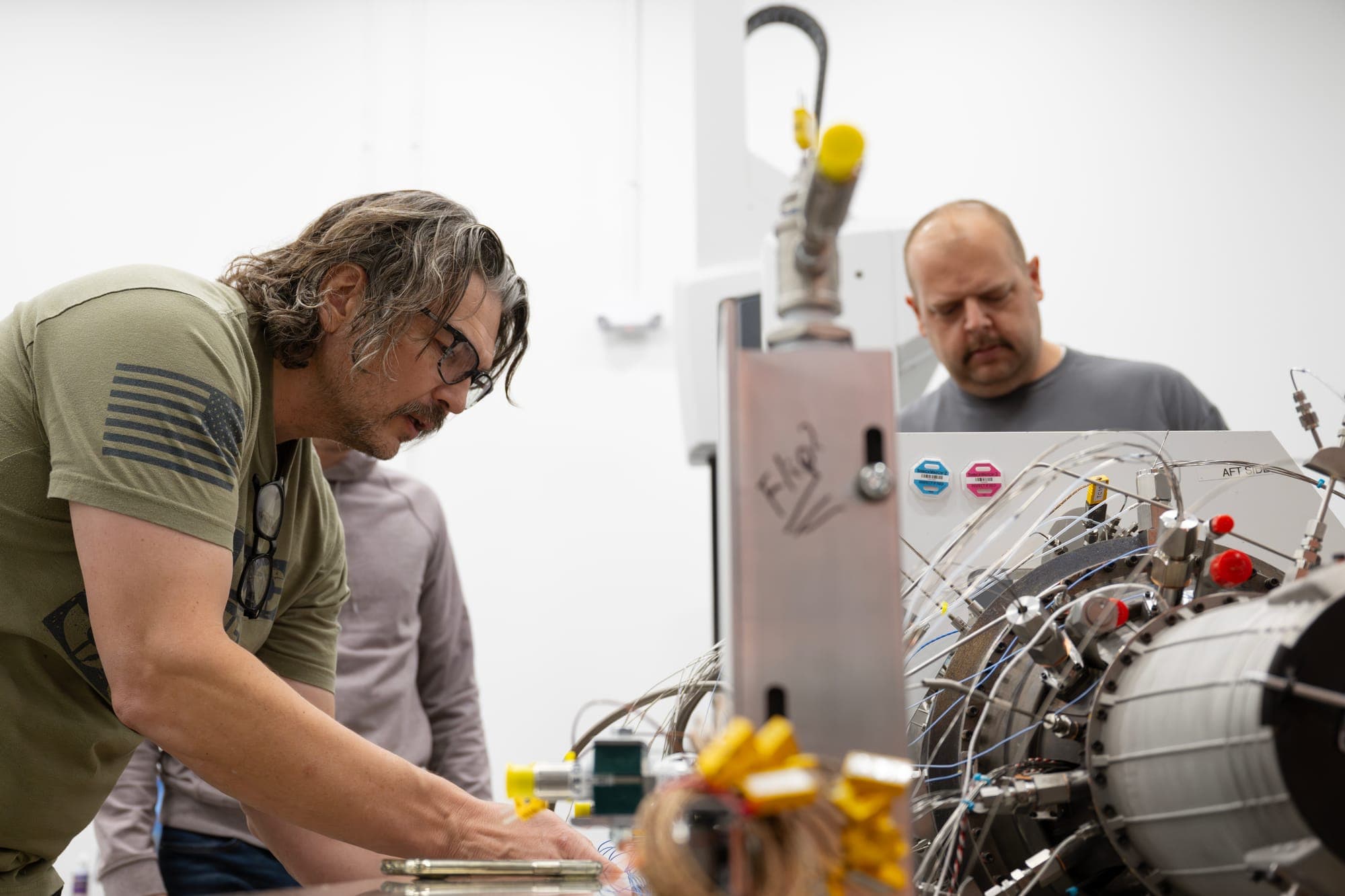
For Eric Donovan, Director of Propulsion Analysis at Beehive Industries®, the role is meant to be. The 22-year aerospace industry veteran recognized the possibilities of additive manufacturing for propulsion early on. Like many of his Beehive colleagues, he contemplated the possibilities for additive before the technology existed to make it possible.
The type of additive manufacturing Donovan mulled over has now become a reality.
The team is harnessing the power of additive manufacturing and advanced computing, and transforming the way jet engines are designed, manufactured, and brought to market. The unique features of Beehive's engine, made possible by this technology, are a testament to the team's innovation and the potential of additive manufacturing in the aerospace industry.
“The best aspect of my role at Beehive is seeing this team use additive manufacturing technology to accomplish what wasn’t possible just five years ago,” explains Donovan. “Earlier in my career, we didn’t have the technology to produce complex designs. Now, we do—at Beehive. But we’ve barely scratched the surface of what additive manufacturing can do.”
Donovan is proud to be a team leader at Beehive, developing and building jet engines for unmanned aerial defense applications.
“At Beehive, we’re using additive manufacturing technology to design an engine tailored to the exact specifications the customer needs and wants,” explains Donovan. “We’re taking advantage of additive to lower prices and reduce the barrier to entry for small to midsize jet engines.”
Eric Donovan's focus extends beyond fluids and thermals. He recognizes that additive manufacturing is bringing about long-overdue changes in the aerospace industry. This technology is unlocking a host of benefits, including cost reduction, compressed design cycles, improved performance, reduced production time, and the ability to scale rapidly to meet immediate and urgent needs. These advantages are reshaping the industry and paving the way for future innovations.
“The industry hasn’t seen a new gas turbine engine for decades, let alone one manufactured with additive manufacturing,” continues Donovan. “This technology can build complexity into a design and offer features that offer significant advantages over traditional engines. It’s a design that works.”
Team building is at the core of engine development
Like any team striving to innovate and advance change, adaptability is key.
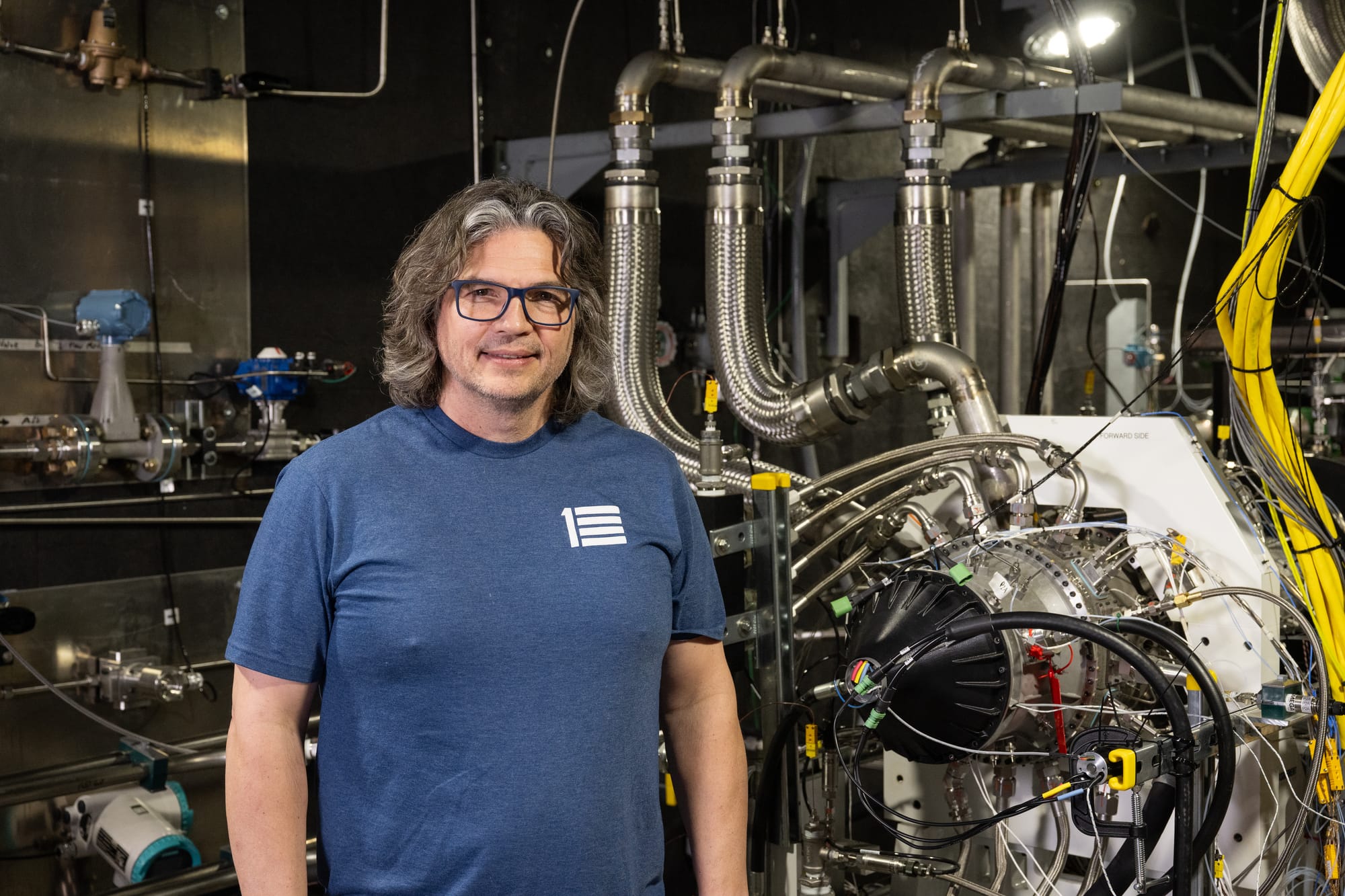
At Beehive, Donovan fosters a culture of collaboration. He brings together engineers from diverse backgrounds and personalities, uniting them under the common goal of advancing the company's mission. His support extends beyond technical expertise, as he helps them navigate the challenges of working in a new environment with new technology.
For engineers, the rapid pace of development and the ability to print and test quickly are a mind shift. To move quickly, it takes ruthless prioritization and overcoming doubts, including self-doubt.
“We all suffer from some insecurities, even engineers who have spent years in aerospace,” said Donovan. “Some call it impostor syndrome. But seeing it all come together at Beehive, you know that you’re meant to be part of the team. When I saw the engine in the test cell, I knew I was in the right place.”
Unlike traditional manufacturing, the Beehive team works in tandem with design, testing, and manufacturing. With additive manufacturing, the team can design, print, and test a component simultaneously, effectively changing how engineers work. Experts in propulsion systems sit next to additive manufacturing experts, partnering with specialists in metallurgy who also bring a wealth of knowledge.
At Beehive’s Colorado headquarters, manufacturing and testing are next to each other. It takes 30 seconds to walk over and see the printers building jet engine components. Teams can collaborate and gain insights into how different teams work. Most importantly, all teams are on hand to provide instant data and feedback. Everyone can see the two jet engine test cells ready and waiting.
Being part of the team advancing aerospace and achieving a “first” makes Donovan smile from ear to ear. “My absolute favorite part of this job is making something happen that never happened before. With the first tests completed, we can tell the world more about what we’ve done.”