Putting an Engine Through its Paces with Russell White
Beehive’s engineering teams test the BTJ-500 jet engine in a custom-built test cell.
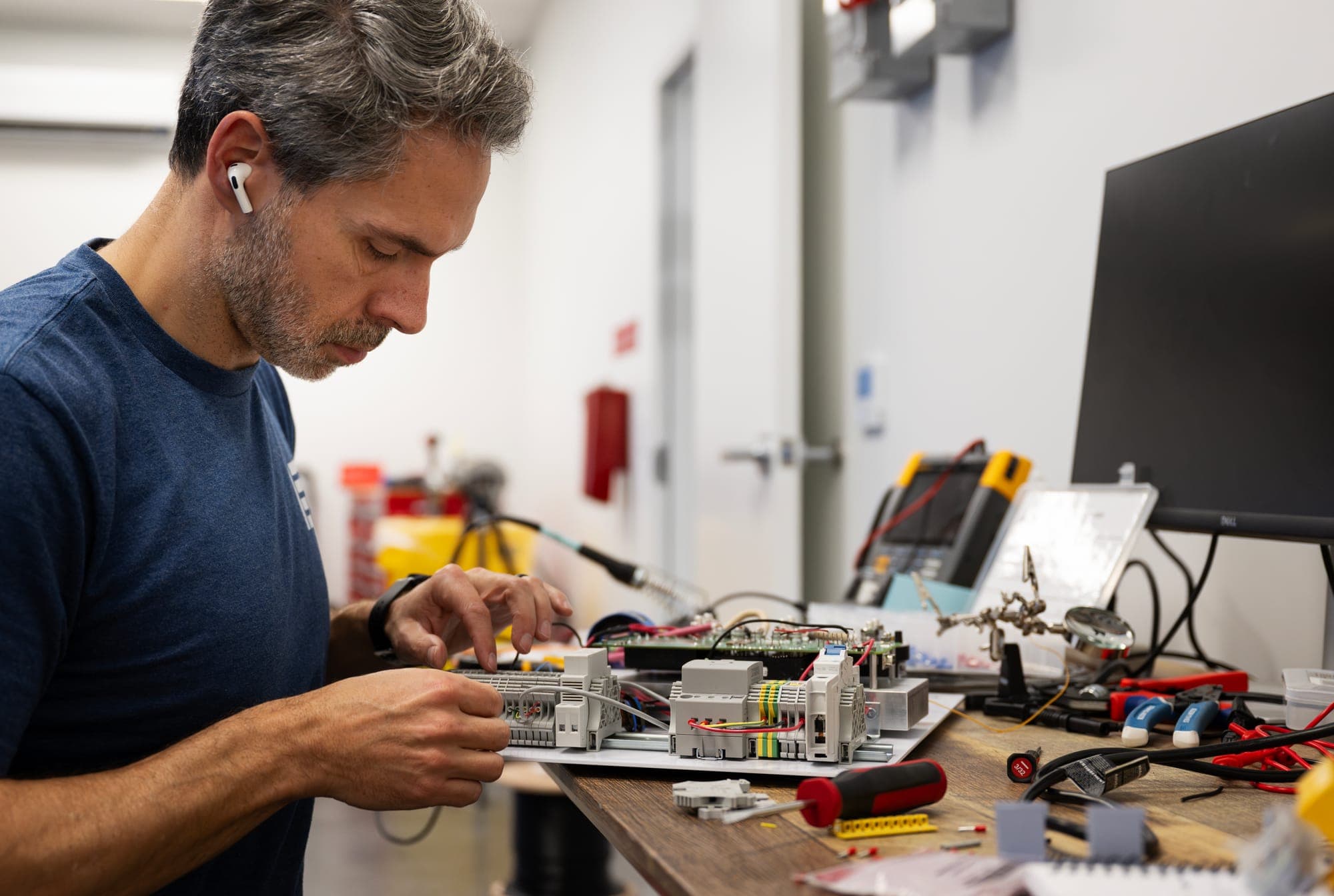
For Russell White, who leads the test and controls program for Beehive Industries, testing a jet engine is like a final exam. “We’ve prepared to the fullest extent, and now it’s time for physics to tell us if our analysis is correct.”
White, a key figure in Beehive's engineering team, has played a pivotal role in developing the company’s groundbreaking 500 lb thrust jet engine demonstrator. This engine, a testament to Beehive's innovative spirit, is designed and built with additive manufacturing—3D printing. The team is subjecting it to rigorous testing at the company’s Denver headquarters.
White’s role is two-fold. He leads the controls group that architects, designs, and develops the control system for the engine. His team is also responsible for developing test cells for Beehive’s suite of jet propulsion systems. His team developed and commissioned the test cell in tandem with the engine control system, and the two processes kept pace.
The adventure of additive
“The past year has been an adventure,” explains White. “Before Beehive, I worked in a more traditional engineering environment where the design and procurement cycle had more constraints and moved at a slower pace. Joining Beehive required me to embrace change and adapt. It’s been an amazing learning experience.”
Additive manufacturing provided a host of advantages to Beehive during the design and production of the engine.
“Thanks to additive, we integrated features and combined functions that aren’t normally combined in gas turbine engines,” explains White. “We reduced the number of parts while providing a more robust system and enhanced performance.”
White provided two examples. First, the engine's compressor has unique features that are only possible with additive manufacturing. Second, the front compressor case is one integrated part. The sump, struts, and vanes, which would be multiple separate parts in a traditional gas turbine engine, are now one part.
Advancements like these, made possible by additive manufacturing, dramatically reduced the number of total engine parts. This manufacturing technology enables shorter production time, opens up the design space for innovation, and enhances performance reducing costs. This flexible design space and ability to rapidly iterate on designs is a testament to the power of additive manufacturing in jet engine technology.
Building engines, from start to finish
Test cells, which take about a year to complete, are where the development engine’s “entrance exam” takes place. These specialized cells, designed and commissioned by White's team, are crucial for testing the engine's performance, safety, and reliability. With the first engine assembled, White’s team installed it in the test cell, ensuring that all systems in the test cell worked, and then started a gradual series of tests, including first fire.
At the same time, White’s team is already working on another engine. The scope and variety of his role are what he enjoys most about working at Beehive.
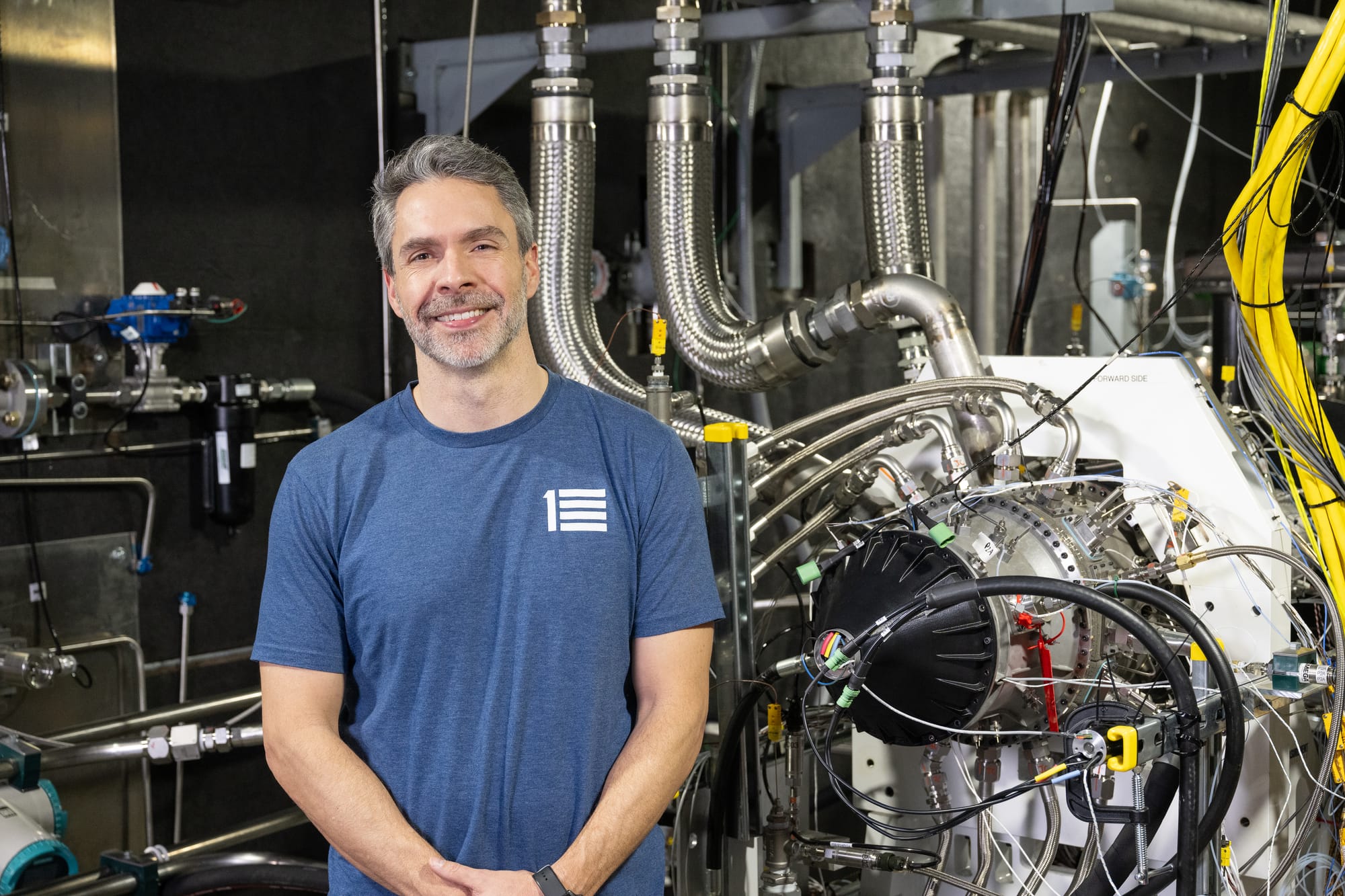
“My team and I, we’re not just designing a jet engine. We're bringing it through the entire design process, from concept to production to testing. Unlike larger, more compartmentalized organizations, you don’t just design and hand off a part to another team. You see the engine through its entire life cycle. Being part of all aspects of engine design and manufacturing is unique to Beehive, and what makes it exciting and challenging for engineering teams.”
At Beehive, engineering teams are also moving at a rapid pace. As a result of additive and the ability to rapidly iterate and test, they can move faster than traditional OEMs. “Designing, building, assembling, and testing an engine in just over a year is a feat for engineering. But what’s most exciting is that we’re already working on another engine. We’re exploring the operating envelope even further, pushing the boundaries of what we thought possible.”
Beehive’s next engine, part of a suite of custom-made propulsion systems, intends to change the game for unmanned aerial applications. More announcements will follow.