Jet Engines and Additive: A Future of Possibilities
Additive manufacturing’s best use-case scenario is propulsion for unmanned vehicles.
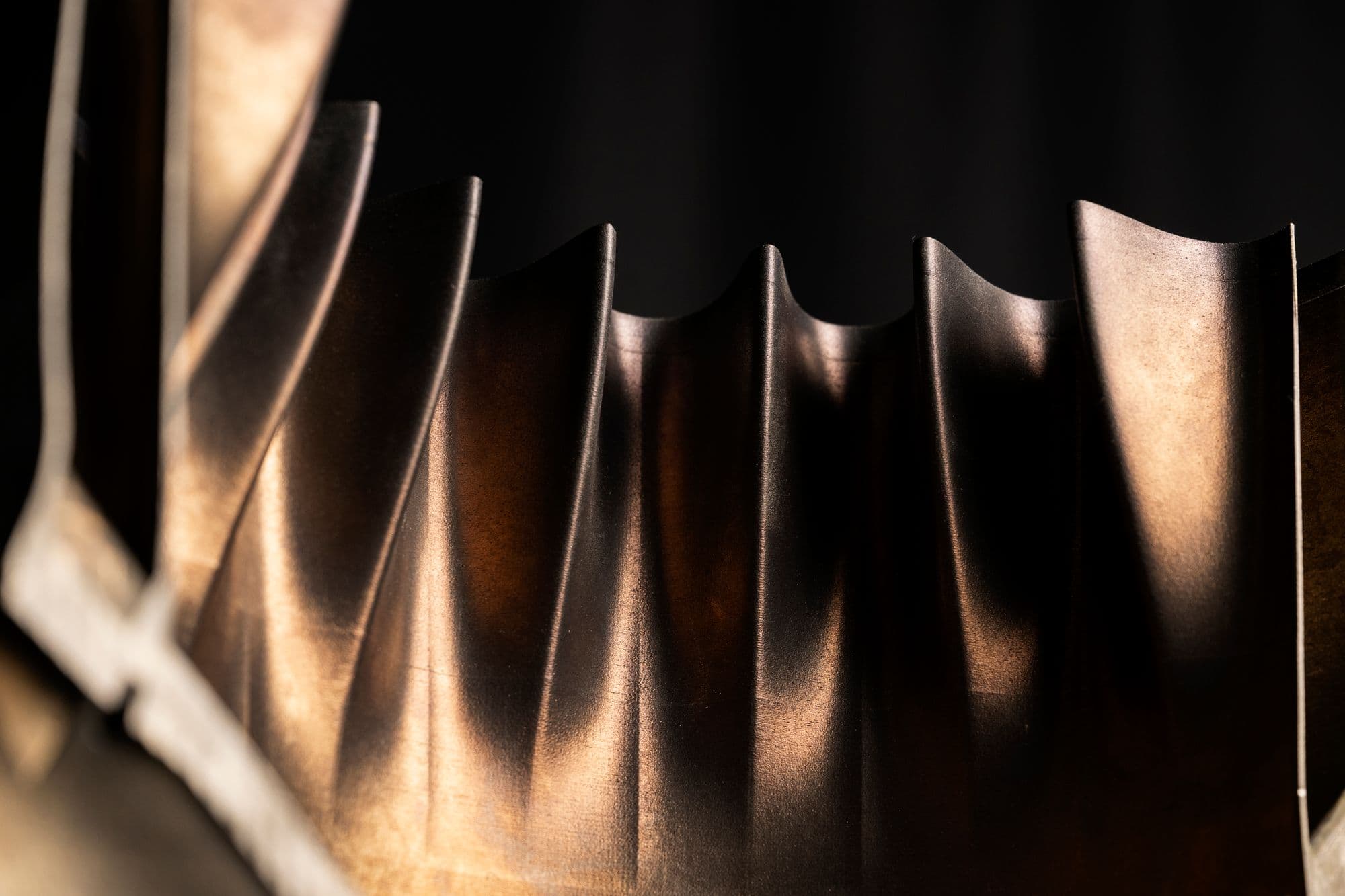
For Beehive Industries’ Gordie Follin, there’s no better time to work in American manufacturing, especially additive manufacturing.
Follin, who has designed and built jet engines for more than 20 years, sees additive manufacturing as a unique opportunity to leverage new technology to its fullest extent. He believes it can unlock the future of new propulsion systems. We sat down with Follin to take a deep dive into Beehive Industries’ engine manufacturing process and learn more about its jet engine, which is built and designed for unmanned aerial vehicles that are expendable, attritable, or exquisite.
What inspired you to join Beehive Industries?
I’ve worked in jet engines my whole career—on the engineering side, on the project management side, and now developing new 3D-printed engines. At Beehive, I saw a unique opportunity to take additive manufacturing and apply it for defense purposes, developing a new propulsion system for unmanned aircraft, including munitions and drones.
Beehive brings together experts who form a bridge between additive manufacturing and propulsion. This combination of talent, expertise, and experience yields the most value as a team, allowing us to solve tough problems. Together, we determined that unmanned propulsion is the best place to deploy these talents. The result is Beehive’s jet engine.
What makes Beehive Industries unique?
Think of Beehive’s four areas of focused expertise, which bridge several industries.
- We have a wealth of traditional jet engine design experience across all levels of the organization.
- We have deep additive manufacturing expertise and capabilities. We are experts in using additive to solve complex design problems.
- We have established a 100% U.S.-based vertically integrated supply chain, with close to 95% of design, testing and manufacturing done in-house.
- We focus on purpose-designed unmanned applications, such as drones.
Combined, Beehive delivers best-in-class performance at best-in-class cost. Our jet engine can offer 10 to 30% better performance, at 50% of the cost, in half the design and manufacturing time.
Why design for attritable, unmanned propulsion?
Let’s take a step back and consider how the aerospace industry has developed jet engines for more than 80 years. The focus was always on engines that transport people. The result constrained the scope of work for anyone who works in jet engine manufacturing. It's driven by safety, and that prime directive drives procedures, as well as a rigid way of approaching design, testing, and costs.
Traditional manufacturing is often locked into a way of doing things, and it tends to curtail agile thinking, cost-savings, and innovation.
At Beehive, we have an additive-first approach. And, when we began designing jet engines for unmanned aircraft, it opened up many new possibilities. We’re not designing a conventional product in a conventional way, so there’s room for new approaches and innovation.
It’s what excites me most about Beehive: the opportunity to approach design challenges from a different angle and not be held back by outdated—or in this case irrelevant—processes and procedures.
Tell us about the additive design process.
Consider that the greatest difference between additive and conventional manufacturing is time. Almost any additive design process will be faster. At Beehive, our process from concept to jet engine tests is about 14 months. That’s close to half the time, or even a third of the time, as conventional jet engine manufacturing.
Several key differences make this possible.
First, our focus is solely on unmanned systems, which have different requirements than commercial aviation. Second, we reach the component testing phase much faster, and can mature the design very quickly. For example, we completed engine component testing and controls testing on our BTJ-500 jet engine in less than 3 months. It’s a 500 lb demonstrator that can support products with up to 5,000 lbs of thrust. For a conventional engine manufacturer, the timeline would be around 14 to 18 months.
With additive manufacturing, we are also hardware-ready. We begin testing within 3 months. As a result, we get data at 3 months instead of 14 months. By the time Beehive reaches engine tests, we are at revision 5 or 6. At that point with conventional manufacturing, you would only reach version 2.
Validation through testing
Additive manufacturing enables design validation through actual testing versus analysis, which can be slower and not necessarily as accurate.
Test data doesn’t lie. Additive allows you to start testing much sooner, which helps you achieve final designs faster.
At Beehive, we use additive to accelerate the process. We also deploy additive to print instrumentation, which provides additional speed and flexibility benefits. When you can print the instrumentation needed for testing, or print the instrumentation into the part, you can tweak the design very quickly.
Building a U.S.-based supply chain
Supply chains by their very nature are global. As a result, there will always be the chance—if not the likelihood—that deteriorating relations between countries, security threats, as well as natural disasters and weather events, will result in a manufacturer not receiving the parts and materials required for critical industries, such as energy or defense.
We’ve heard a lot about this in recent years, and the need for a strong U.S.-based supply chain continues to be present. Government agencies, which by their very nature require a secure U.S.-based supply chain, are looking to additive manufacturing to solve this problem.
With additive, a U.S.-based manufacturer can literally bring metal powder in one door of their facility and take a finished product out the other door. Our engines are almost entirely manufactured within a single facility. We can do this because we have consolidated parts and simplified engine design. And, we print with powder. We have far fewer suppliers, and those suppliers are in the U.S., which means less chance of disruption.
Consider that each part of an engine is something that could go wrong. So, the fewer dependencies that you have within a global network, the more secure your supply chain. Additive manufacturing requires fewer parts, which de-escalates risk at scale.
Forward-deployable technology
An unsung benefit of additive manufacturing is that it’s forward deployable: You can move it.
Once you lock in design, then print and test successfully, it’s relatively easy to both scale and physically move manufacturing. Unlike conventional manufacturing, which relies on foundries and specialized labor, additive manufacturing is not tied to a specific facility or location. Think of it as rapidly moving the supply chain. Unlike a foundry, it’s comparatively easy to move printers and metal powders.
And, it’s rapidly scalable. Beehive can scale up manufacturing of our engines quickly. For example, in a small portion of one of our three facilities, we can manufacture close to 2,500 engines per year.
What’s next for Beehive?
By bringing together jet engine and additive manufacturing expertise, focusing on unmanned applications, and building a vertically integrated supply chain, we believe we’re building the right process for the right application at the right time.
The result is a best-in-class solution for unmanned aerial systems. We’re continuing to innovate and accelerate development, while also partnering with our customers to develop bespoke jet engines that harness the full potential of additive manufacturing.