Delivering the Speed the Market Needs: David Kimball Gets It Done at Beehive Industries®
For VP of Engineering, it all comes down to the union of best-in-class teams with breakthrough technologies.
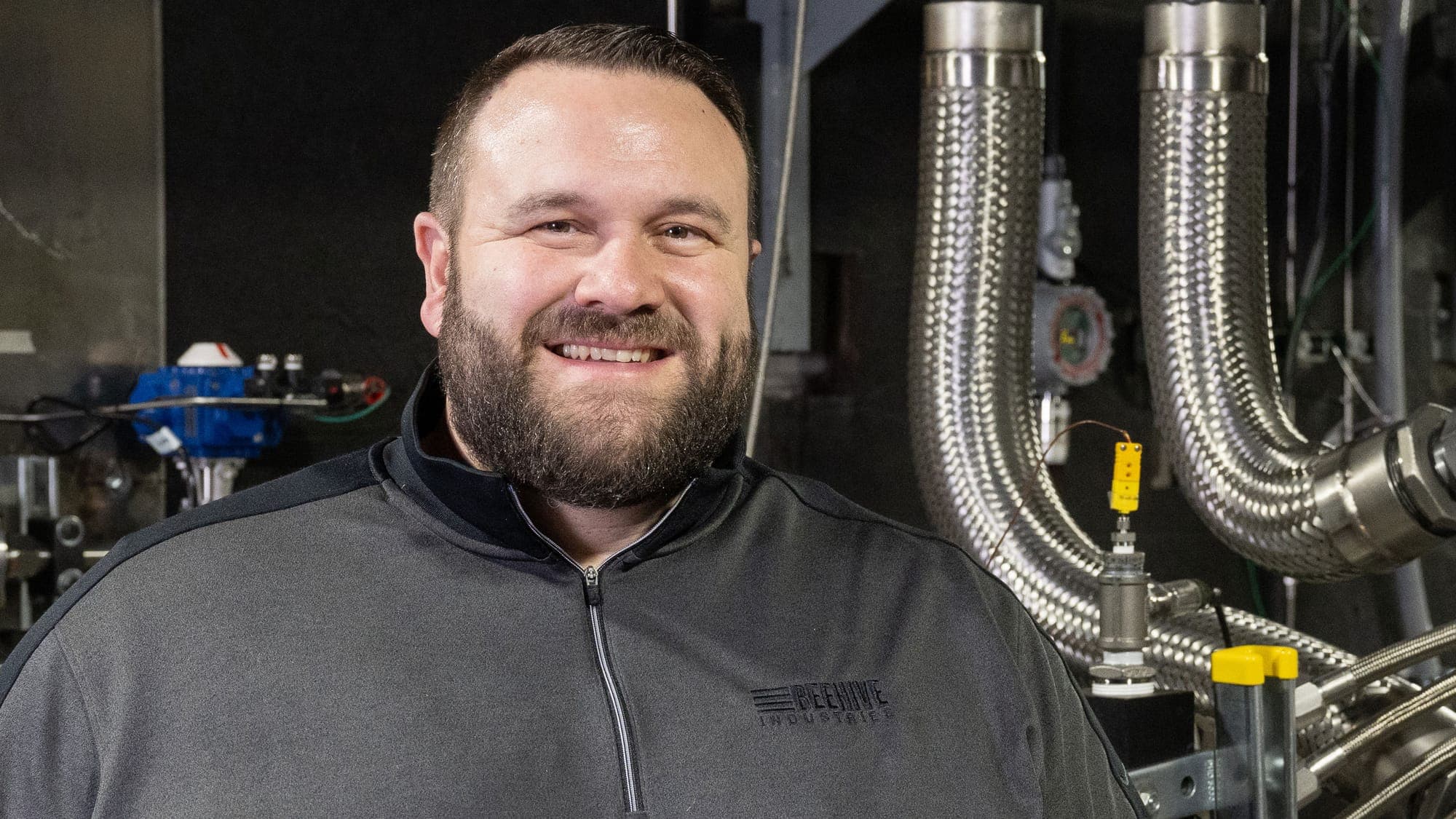
David Kimball is standing next to a jet engine he once thought impossible to build. It’s the Beehive Industries® 500 lbf demonstrator, and it’s ready in a test cell. As VP of Engineering at Beehive, Kimball is part of the team that brought a brand new, clean sheet design to ready-to-test in less than 13 months. He attributes this achievement to Beehive’s people and mission.
Kimball’s role at Beehive is to inspire engineering teams to find innovative technical solutions to some of the world’s toughest challenges. They’re doing it with additive manufacturing—3D printing—and a host of new technologies that weren’t available during the earlier years of his career.
Getting it done with additive manufacturing
Beehive is responding to a market need to deliver jet engines faster and at much lower cost—engines that provide the performance required by the Department of Defense. Built with additively enabled technology, these jet engines allow for unprecedented performance, delivered in half the time and for half the price.
Kimball breaks down Beehive’s advantages as 1) performance, 2) lower cost, and 3) reduced time to design and deliver. It’s the speed the market needs.
“The macro environment for defense is constantly changing,” explains Kimball. “We see conflicts erupting worldwide and have instances where we need to provide deterrents. The Department of Defense needs solutions delivered faster to meet their requirements and at a significantly lower cost.”
Kimball is proud of his team's work, and their determination to push boundaries.
A game changer for jet engine manufacturing
“At Beehive, we’re delivering jet engines in a way that’s never been done before in our industry,” said Kimball. “We’re doing something that, at one point, we all thought was impossible. Now, we’re making it possible. That’s a game changer for jet engine manufacturing and for each of us as individuals. As engineers, we’re realizing new possibilities as a team. We faced challenges, but through our collaborative efforts, we overcame them.”
“We're committed to continuous improvement,” Kimball continued. We’ve gone from a clean-sheet design to testing in a short period, and now we're putting the engine through its paces. The tests not only help us understand its performance at a fundamental level but also identify areas for improvement. We’re confident in our design, but we're always looking for ways to enhance performance. We’re also refining production time and will incorporate these learnings into mass production.”
The team is testing the jet engine at Beehive's Denver headquarters in a test cell they built on-site. The series of tests analyzes how the compressor, combustor, and turbine all function together. Most importantly, the tests determine if the engine delivers the performance Beehive customers need. The process delivers market-ready engines within a timeframe that’s never been done before.
With an eye on a future suite of jet engines, the team is not only creating a blueprint for delivering additively enabled engines on a larger scale but also paving the way for future advancements in engine technology. Ramping up production to several engines a day is within sight.
The people who made it happen
“I’m incredibly proud of this team,” concludes Kimball. “This is exciting yet challenging work, and everyone at Beehive inspires me. We have different backgrounds, ranging from working with large OEMs to small startups, and that offers a diversity of perspectives. It energizes me.”
Kimball concludes by sharing a memory from a customer tour of the Denver facility, “We were on the shop floor while a tour was underway with high-level executives. The engineers were part of the tour, engaging and answering questions with manufacturing. We’re all equals, sharing knowledge and enthusiasm for the work underway. One of my colleagues turned to me and said that this level of interaction and teamwork—between customers, engineers, and operations—would never happen anywhere else. And that summed up Beehive for me. We’re doing something that was once impossible, and we’re doing it in a collaborative and different way. The technology makes it possible, but the Beehive team is making it happen. Our people are the differentiators.”