Building the Path Forward for Additive Manufacturing
The transition from castings and forgings to additive manufacturing offers a wealth of opportunities for the U.S. manufacturing sector.
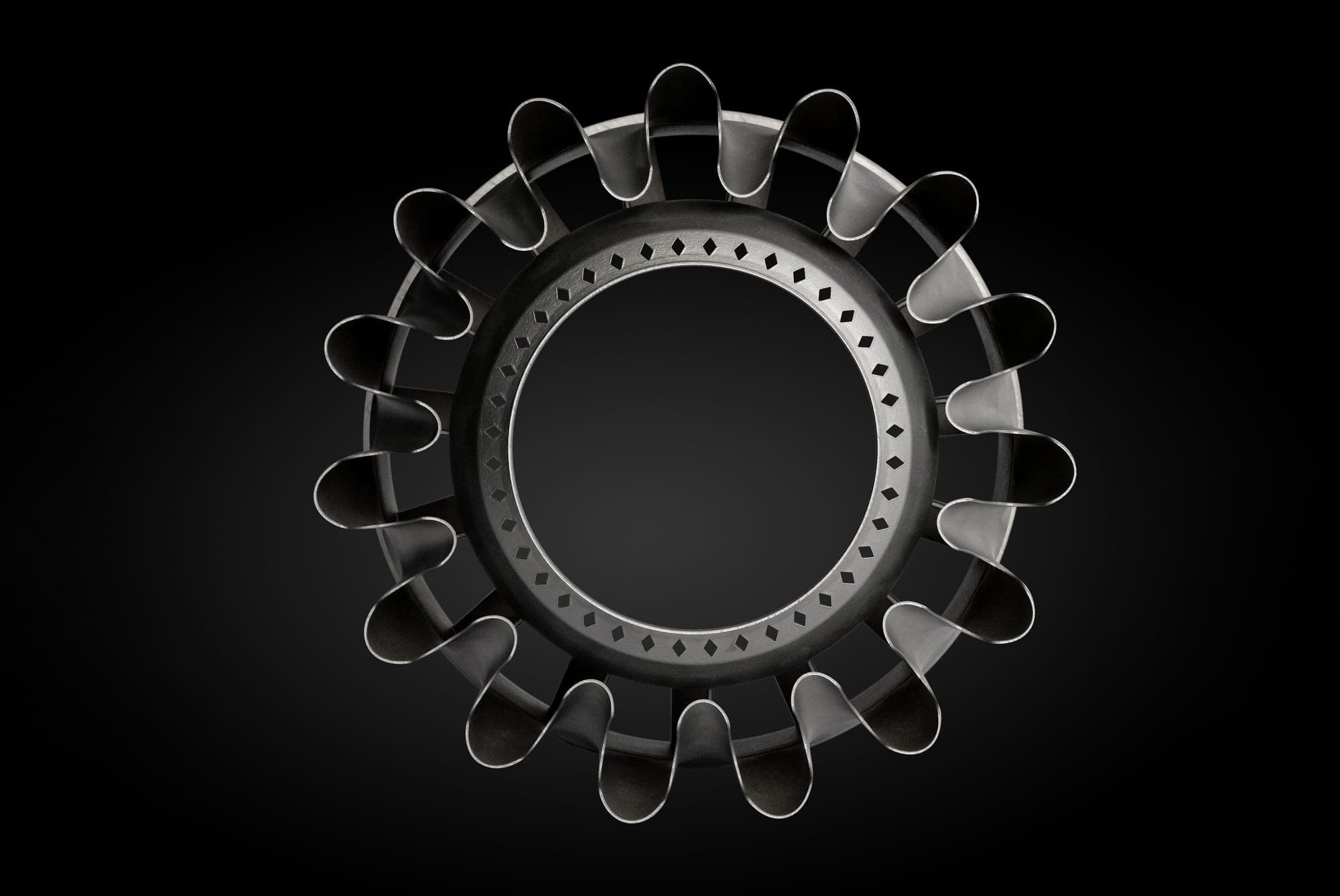
For Beehive Industries’ Jonaaron Jones, additive manufacturing is the future of American manufacturing.
From new superalloys to extended design capabilities, American manufacturing has barely seen the tip of the iceberg for additive manufacturing. As Chief Manufacturing Technology Officer, Jones has a unique viewpoint of the industry’s untapped opportunities. We sat down with him to explore the innovation underway at Beehive, how traditional manufacturing can take advantage of additive manufacturing, and what most excites him about the future of American manufacturing.
What’s your role at Beehive Industries?
I lead the Manufacturing Technologies group at Beehive. My primary focus is supporting our customers by delivering manufacturing solutions and guidance for our production and design teams.
There’s also a research and development aspect to our work because, for many of our customers, this is their initial use of additive manufacturing. They come to Beehive to determine what’s possible for their organization. My team works in lockstep with them to identify improvements that translate into shorter lead times, improved performance, and higher quality parts.
What’s the toughest challenge customers bring to Beehive?
The toughest challenge is twofold: it’s the desire for greater performance, such as higher operating temperature capabilities, and the need for rapid production. We partner with them to test and develop new superalloys that enable both.
For example, we’re offsetting traditional castings that are long-lead items for our industrial gas turbine customers.
All gas turbines have regular maintenance intervals that require operators to take their gas turbines offline, remove parts, and replace them. But in many cases, the lead time on critical items can be in excess of 1-2 years. Castings and forgings are incredibly long-lead items. It’s unpredictable and there’s no guarantee that you’ll get the parts you need in the optimal time frame.
Beehive offers the answer. We can make those parts with additive manufacturing in a fraction of the time and at a competitive cost.
Enhancing capabilities and performance
Speed is only one part of the equation.
Beehive is also developing printable superalloys to meet the need for enhanced capabilities and performance.
For most customer applications, additive manufacturers use more traditional materials like nickel alloys 718 and 625, which are highly weldable and easier to work with. However, these traditional alloys have limitations, including strength and heat resistance. To address these limitations, Beehive is adapting new superalloys for use in the additive manufacturing processes.
Of course, saying that is easy. Doing it is entirely different.
At Beehive, we bring together experts and specialists who might otherwise be siloed; we have a strong team that includes academic metallurgists, a range of engineering specialists, and others who bring a unique understanding or approach. We bring this diversity of experiences and perspectives together in a collaborative setting and encourage them to continuously test/print material samples.
And when I say samples, I mean lots of samples.
The process looks like this: We cross-section samples, polish the surface, look at it under a microscope, and characterize what we see. Do we see pores or cracks? What are their shapes and sizes?
Then, we modify conditions, increase or slow velocity, etc. We explore everything we can to change the process. We might make 100 samples to look for trends.
It's a highly iterative process: explore and discover, then more exploration and discovery. The combined team looks deeper to identify what’s causing issues. It’s through this process, and the bringing together of a range of expertise, that we achieved success.
Tell us more about these new superalloys.
At Beehive, we’re working with alloys that exist on the border of higher performance and challenging weldability. Additively manufactured parts are also closer to being usable right out of the printer, so the process is very different.
Because of the unique way we process materials with additive manufacturing, we can melt and cool them very quickly. As a result, we can tailor microstructures and potentially suppress their tendency to crack. This opens the door to a new and better additively printed superalloy.
Our ongoing goal is to offer our customers the most capable and challenging materials to support their needs. The result, so far, is the release of three new superalloys:
- Mar-M 509, which several Beehive customers are using today
- Inconel 939
- Mar-M 247
Mar M-247 was originally an internal challenge, an aspirational goal. Our success is a reflection of the Beehive team’s unrelenting drive to find solutions through traditional metallurgy and through innovative ideas.
Where do you see the greatest potential for additive manufacturing?
The tipping point will come when industries start designing to take advantage of additive manufacturing. Today, most manufacturers are taking traditional design, materials, and specifications that have existed for years and adapting them to additive manufacturing. The next phase will be designing with additive manufacturing specifically in mind, which could ultimately result in a very different product with fewer parts and increased performance and reliability.
But, designing for additive manufacturing and higher performing metal alloys will require a change in mindset.
What use scenarios are emerging?
There are two big picture opportunities for additive manufacturing.
First, there are a multitude of parts in existence that have become increasingly hard to get castings and forgings for. Additive manufacturing can be a viable option to help bring down lead times and provide solutions for defunct vendors. That’s a game changer.
Second, and this is the greatest opportunity, manufacturers are beginning to design for additive manufacturing. In the near future, castings and forgings will not be the only option for performance critical hardware.
Beehive’s jet engines are an example of designing with additive manufacturing in mind. They were designed from the outset to take advantage of the benefits offered by additive manufacturing, rendering them significantly different from traditional jet engines. There is simply no other way to manufacture most of Beehive’s engine components other than additive manufacturing.
That approach—designing for additive manufacturing—is unlocking all kinds of potential.
How quickly is manufacturing shifting toward additive manufacturing?
Until recently, much of the demand for additive manufacturing was printing a part originally designed for castings and forgings. It’s a go-to option when there’s urgency. That’s why many companies decide to use additive manufacturing: they have an unanticipated need to procure high-quality parts within a short time window.
But, as manufacturers see the benefit of the speed that additive offers, they also realize they are missing out on potential performance gains as well. The conclusion most reach is that additive manufacturing can offer them much more.
We’re now entering a new phase in which companies are exploring how to design for additive manufacturing and take advantage of new materials, in addition to the speed of design and production.
What will it take for more companies to make that mindshift?
There are a lot of factors coming into play that are triggering this shift. In some cases, it’s seeing the value of additive manufacturing proven out in other industries—we have excellent use case scenarios to help guide decision-making.
There may also be pain points that drive more decision making toward additive manufacturing. If you have equipment, services, aircraft—you name it—that are taken offline due to parts shortages or delays, you will look for solutions.
The education of engineers will also make an impact. When additive manufacturing is a fundamental aspect of your training, as it is in many engineering schools today, you will have an advantageous mindset.
The Department of Defense’s purchasing cycles may also accelerate the shift. For example, a recent helicopter competition encouraged the use of new technologies, especially additive manufacturing. One company reached out to Beehive to integrate additively manufactured parts into their design. As a result, they compressed a two-year procurement cycle into one, providing them with a competitive edge.
But, bear in mind that this is more than a mindshift or a commitment to process improvements. Certification is one of the biggest hurdles to wider adoption.
Currently, there isn’t a plethora of well-understood, well-documented industry standards. But, we’re making significant and rapid progress. The Department of Defense is taking a leadership role in establishing policy and guidance, which will flow down to the manufacturing base, establishing a MIL-SPEC that’s all-inclusive. This is important work that will contribute to the continued adoption of additive manufacturing in the American manufacturing sector and beyond.
Additive manufacturing is still young. While many manufacturers have embraced its potential, we are at the beginning of a wave of innovation. I anticipate that the development of industry specific materials and specifications will accelerate the use of additive manufacturing in the very near future, and a new age of innovation will follow.